The global shift toward electric vehicles (EVs) and renewable energy has created a pressing challenge: what happens to lithium-ion batteries once they reach end-of-life? Enter black mass battery recycling—a critical process for recovering high-value metals like cobalt, nickel, and lithium from spent batteries. For businesses committed to sustainability and circular economies, understanding black mass recycling is no longer optional—it’s essential.
What Is Black Mass in Battery Recycling?
Black mass is the term for the shredded, processed material derived from spent lithium-ion batteries. It contains a concentrated mix of valuable metals, including lithium (Li), cobalt (Co), nickel (Ni), and manganese (Mn), encased in a carbon-based matrix.
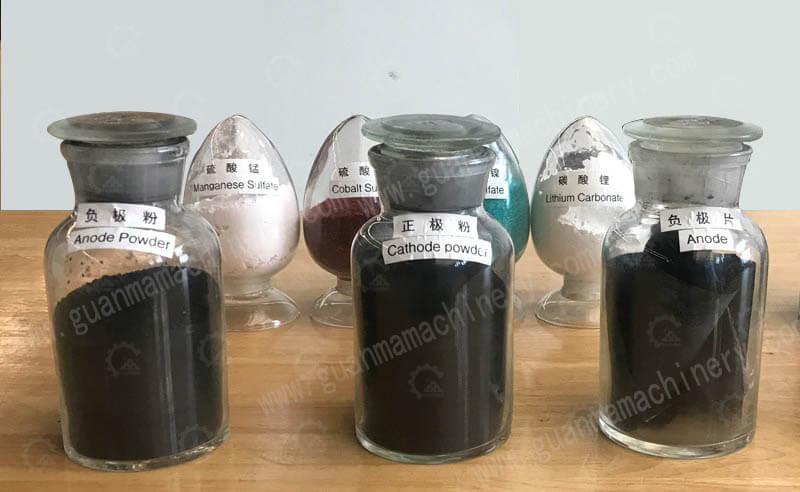
How is black mass produced?
Batteries undergo discharging, dismantling, and mechanical crushing to separate plastics and casings. The remaining material—a powder-like substance—is the black mass, which holds up to 60% of a battery’s critical metals.
The Black Mass Recycling Process: Step-by-Step
Step 1: Battery Collection & Pre-Treatment
End-of-life batteries are safely collected, discharged, and dismantled. Mechanical shredding separates metals, plastics, and black mass.
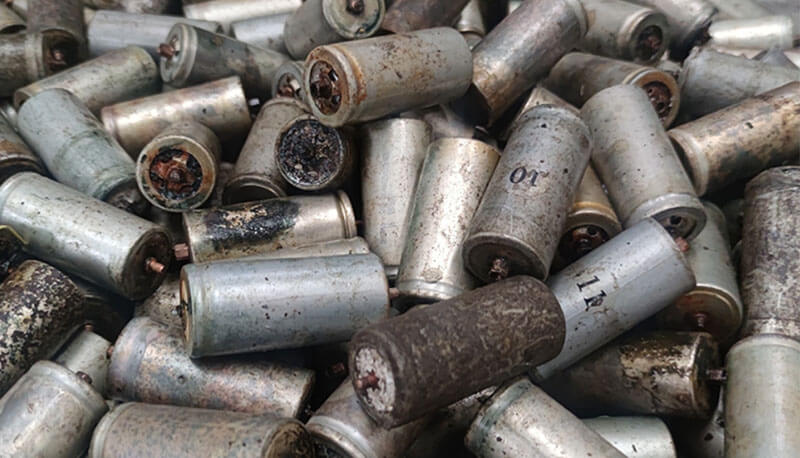
Step 2: Hydrometallurgical or Pyrometallurgical Processing
Hydrometallurgy: Black mass is dissolved in chemical solutions (e.g., acids) to leach out metals. This method achieves 95%+ purity for cobalt and nickel.
Pyrometallurgy: High-temperature smelting extracts metals but often loses lithium.
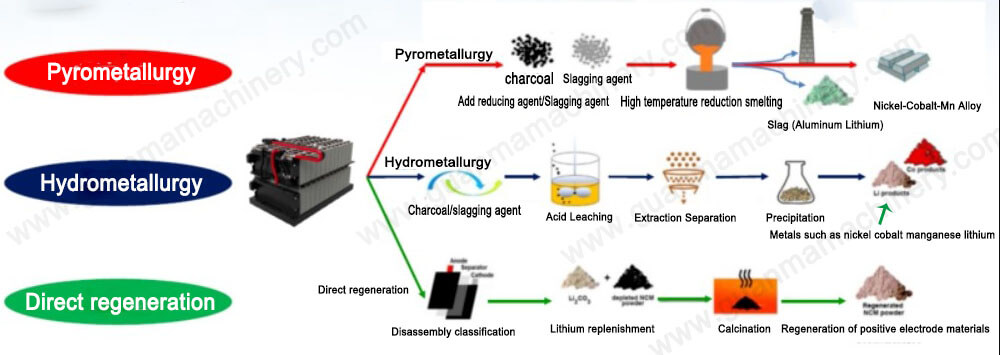
Step 3: Metal Refining & Reuse
Recovered metals are refined into battery-grade materials for new batteries, reducing reliance on mining.
Why Black Mass Recycling Matters for Sustainable Businesses
A. Economic Benefits
Cost savings: Recycling 1 ton of black mass can yield up to $15,000 worth of metals (depending on market prices).
Supply chain security: Mitigates risks from volatile metal prices and geopolitical mining issues.
B. Environmental Impact
Reduces mining demand: Recycling 10,000 EV batteries saves ~50,000 tons of raw ore extraction.
Lowers carbon emissions: Reusing metals generates 70% fewer emissions than virgin mining.
C. Regulatory Compliance
Meets EU Battery Regulation (2023) and U.S. IRA requirements for recycled content in new batteries.
Aligns with ESG (Environmental, Social, Governance) goals for investors and consumers.
Challenges in Black Mass Recycling (And How to Overcome Them)
A. Complex Material Composition
Black mass from different battery types (e.g., NMC, LFP) varies in metal ratios.
Solution: Advanced sorting technologies (AI-powered systems) and flexible chemical processes.
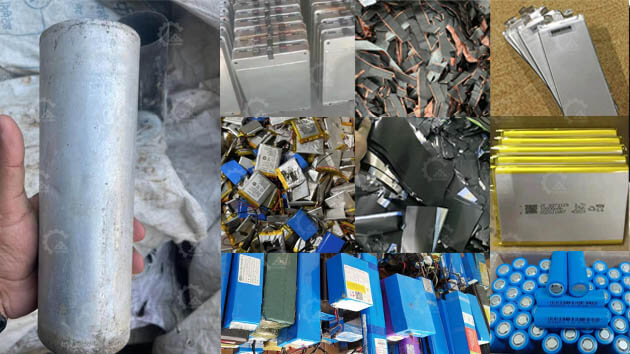
B. Lithium Loss in Traditional Methods
Pyrometallurgy often fails to recover lithium.
Solution: Hydrometallurgical methods with selective leaching agents (e.g., citric acid) preserve lithium yields.
C. Hazardous Waste Management
Chemical solvents and byproducts require careful handling.
Solution: Closed-loop systems and partnerships with certified waste treatment facilities.
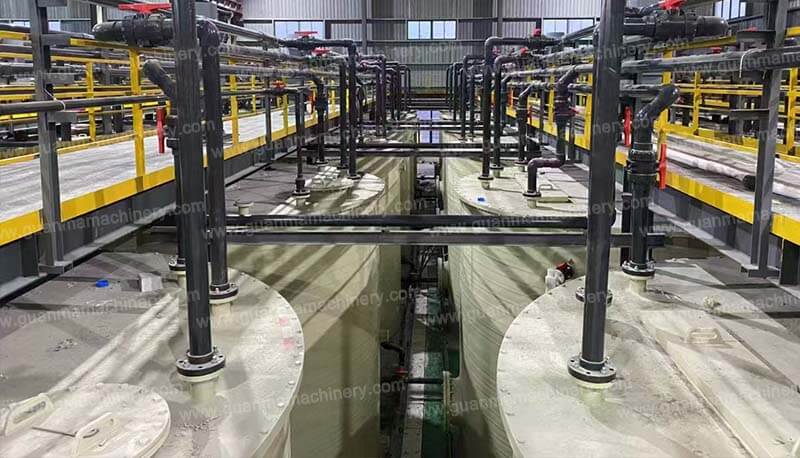
Choosing a Black Mass Recycling Partner: Key Criteria
To maximize ROI and sustainability, partner with recyclers offering:
High recovery rates: >95% for cobalt, nickel, and lithium.
Certifications: R2v3, ISO 14001, or IRMA (Initiative for Responsible Mining Assurance).
Transparent reporting: Detailed analytics on metal yields, carbon savings, and compliance.
The Future of Black Mass Recycling
Direct recycling: Emerging technologies regenerate cathode materials directly from black mass, skipping smelting.
Government incentives: Tax breaks and grants for recycling infrastructure.
Unlock Value and Sustainability with Black Mass Recycling
Black mass battery recycling isn’t just a waste management strategy—it’s a competitive advantage. By recovering critical metals efficiently, businesses can cut costs, meet regulations, and build greener supply chains.