Introduction to Coconut Shell Charcoal Manufacturing Plant
Coconut shell charcoal manufacturing plants are revolutionizing the way we produce charcoal while offering a sustainable, eco-friendly alternative to traditional charcoal production.
These plants use coconut shells, a byproduct of coconut processing, to create charcoal that is highly sought after for both industrial and consumer uses. This article will walk you through the ins and outs of setting up and operating a coconut shell charcoal manufacturing plant, covering everything from the benefits to the processes involved.
What is a Coconut Shell Charcoal Manufacturing Plant?
A coconut shell charcoal manufacturing plant is a facility where coconut shells are processed and converted into charcoal through a process called carbonization. Charcoal made from coconut shells is used in a variety of industries, including agriculture, food production, and environmental protection. The plant uses specialized machinery to heat the shells at high temperatures in the absence of oxygen, turning them into a carbon-rich product that is perfect for different applications.
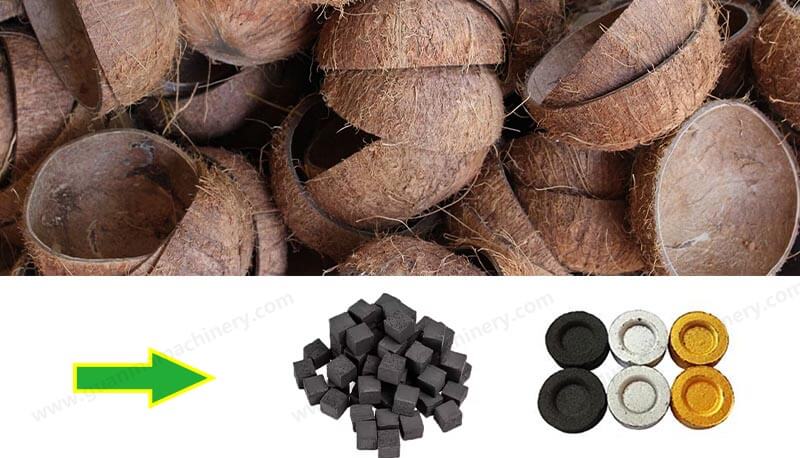
Why is Coconut Shell Charcoal Important?
Coconut shell charcoal is an eco-friendly product because it’s made from natural waste. By using coconut shells, which would otherwise be discarded, the manufacturing process reduces waste and contributes to sustainability. Additionally, coconut shell charcoal has high carbon content, making it an efficient and cleaner-burning alternative to other types of charcoal.
The Process of Manufacturing Coconut Shell Charcoal
Step-by-Step Process
The production of coconut shell charcoal follows a straightforward yet intricate process:
Collection of Coconut Shells: The first step involves collecting coconut shells, which are typically discarded after the coconut is harvested for its water and meat.
Cleaning and Drying: The shells are cleaned and dried to remove any moisture content.
Carbonization: The dried shells are then heated in a carbonization furnace. The temperature in this furnace typically ranges between 400°C and 700°C, and the shells are heated in the absence of oxygen to ensure they do not combust but instead turn into charcoal.
Cooling and Grinding: After carbonization, the charcoal is cooled and crushed into smaller pieces if needed.
Materials Required for the Process
Apart from coconut shells, the manufacturing process requires certain materials such as fuel for heating the furnace and equipment for crushing and grinding the charcoal.
Equipment Used in Coconut Shell Charcoal Production
Carbonization Furnace
A high-efficiency carbonization furnace is the heart of the charcoal manufacturing plant. This furnace ensures that the coconut shells undergo the carbonization process under controlled conditions, turning them into charcoal without combustion.
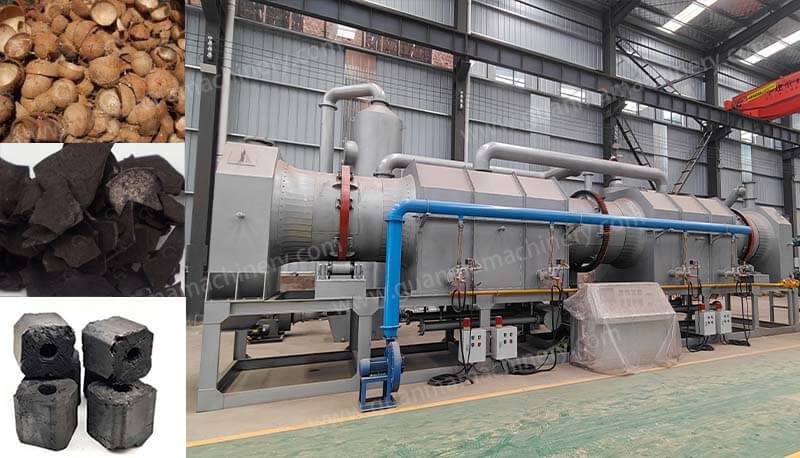
Crushing and Grinding Machines
These machines are used to crush and grind the charcoal into smaller, usable sizes for various applications. Whether it’s for activated charcoal or regular charcoal briquettes, the final product must be finely processed.
Airflow Systems and Filters
Since the carbonization process produces smoke, efficient airflow systems and filters are used to manage emissions and ensure minimal environmental impact.
Selecting the Right Coconut Shell Charcoal Plant for Your Needs
When choosing the right plant, consider factors such as production capacity, budget, and automation level. Each type of plant has its pros and cons, so it’s essential to assess your specific needs before making an investment.
Key Components of a Successful Coconut Shell Charcoal Manufacturing Business
Efficient Raw Material Sourcing
Sourcing high-quality coconut shells at a competitive price is crucial for the success of your business. Establishing good relationships with local coconut farmers can help secure a steady supply.
Energy Management
Since carbonization requires high heat, energy consumption can be significant. Opting for energy-efficient systems or using renewable energy sources like biomass can reduce operational costs and environmental impact.
Waste Management
Incorporating waste management practices into your plant is essential. This includes finding ways to use or recycle the byproducts of the charcoal-making process.
Choosing the Right Supplier for Your Plant
When selecting a supplier for your charcoal plant, ensure they provide reliable, high-quality equipment and have a solid track record of customer service.