Understanding the gold electrolytic refining recovery process is critical for businesses in precious metal recycling, jewelry manufacturing, and electronics scrap processing. This method ensures high-purity gold recovery (up to 99.99%) while minimizing waste and operational costs.
What Is the Gold Electrolytic Refining Recovery Process?
The gold electrolytic refining recovery process is a widely used industrial method to purify raw gold (often sourced from scrap, ores, or recycled materials) using electrolysis. It dissolves impure gold anodes in an electrolyte solution, separating precious metals from base metals and impurities. This process is favored for its precision, scalability, and ability to recover platinum-group metals as byproducts.
7 Steps in the Gold Electrolytic Refining Recovery Process
1. Feed Material Preparation
Raw gold materials (e.g., jewelry scraps, electronic waste) are melted and cast into anode plates. Impurities like copper, silver, or nickel are partially removed through preliminary treatments like acid leaching or cupellation.
2. Electrolyte Solution Setup
A highly conductive electrolyte solution—typically hydrochloric acid (HCl) mixed with gold chloride (AuCl3)—is prepared. The solution’s temperature, pH, and concentration are carefully controlled to ensure optimal ion mobility.
3. Electrolysis Cell Assembly
The impure gold anode and a pure gold cathode are submerged in the electrolyte bath. When an electric current is applied, gold ions (Au³⁺) migrate from the anode to the cathode, depositing as pure gold.
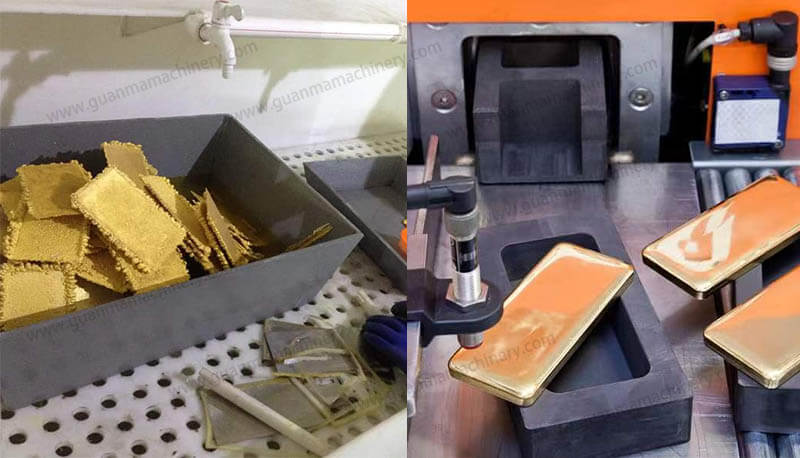
4. Electrolysis Operation
During electrolysis (24–48 hours), base metals (e.g., copper, iron) dissolve into the electrolyte, while precious metals like gold and platinum accumulate on the cathode. Voltage (3–5V) and current density (100–300 A/m²) are adjusted based on anode purity.
5. Sludge Treatment
Impurities settling as anode sludge (containing silver, platinum, or palladium) are filtered, dried, and processed separately to recover additional precious metals.
6. Cathode Gold Harvesting
The cathode, now coated with 99.95%+ pure gold, is removed, washed, and melted into bars or granules for commercial use.
7. Electrolyte Regeneration
The depleted electrolyte is replenished with fresh gold chloride to maintain efficiency, while residual acids are neutralized to meet environmental standards.
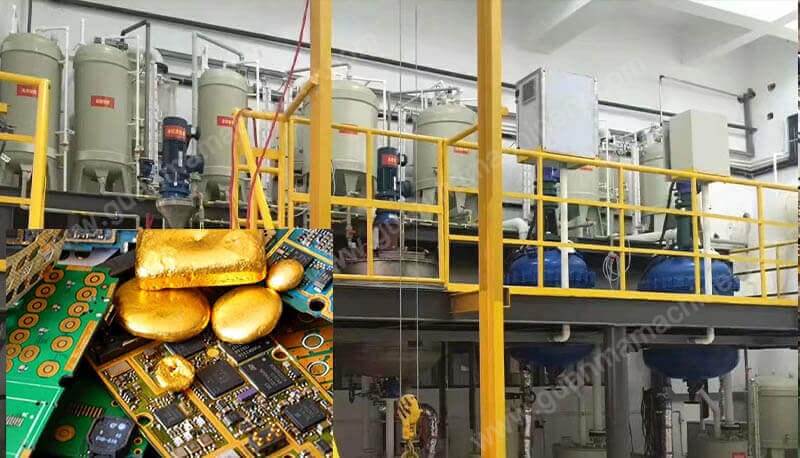
Why Optimize Your Gold Electrolytic Refining System?
Investing in a modern industrial gold electrolytic refining system delivers significant advantages:
Higher Purity: Achieve 99.99% gold purity, meeting LBMA standards for bullion trading.
Cost Efficiency: Reduce gold losses to <0.1% and lower energy consumption by 20–30%.
Byproduct Recovery: Extract platinum, palladium, and silver from anode sludge.
Eco-Friendly Compliance: Minimize toxic emissions with closed-loop electrolyte management.
Advanced Technologies Enhancing the Process
Leading suppliers integrate innovations to address common challenges:
Automated pH Control: Maintains electrolyte stability for consistent deposition rates.
Titanium Cathode Plates: Resistant to corrosion, extending equipment lifespan.
Energy Recovery Systems: Capture waste heat from electrolysis to power auxiliary processes.
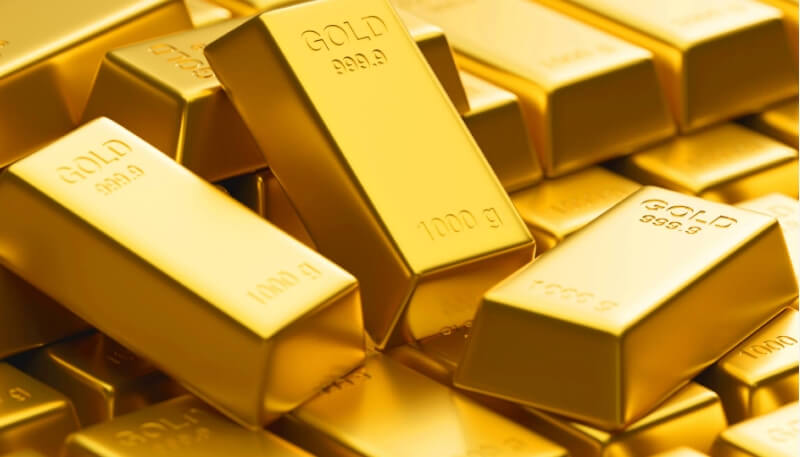
Partner with a Trusted Gold Refining Equipment Supplier
Selecting the right partner is crucial for optimizing your gold electrolytic refining recovery process. Look for suppliers offering:
Customized System Design: Tailored to your feedstock type and production scale.
On-Site Training: Ensure safe and efficient operation of electrolysis cells.
Global Technical Support: Rapid troubleshooting to minimize downtime.
Streamline Your Gold Recovery Workflow
The gold electrolytic refining recovery process remains the gold standard for high-purity metal extraction. By adopting advanced systems and partnering with experienced suppliers, businesses can enhance profitability, sustainability, and compliance in competitive markets.