Are you familiar with Guanma Machinery’s hydrometallurgical recycling process for waste lithium batteries? This method adopts a hydrometallurgical recycling process that integrates and simplifies the process flow, featuring low overall energy consumption and high product recovery rates.
Currently, only lithium iron phosphate batteries can be reused in a cascade manner to utilize their remaining value; whereas ternary lithium batteries are primarily recycled through dismantling.
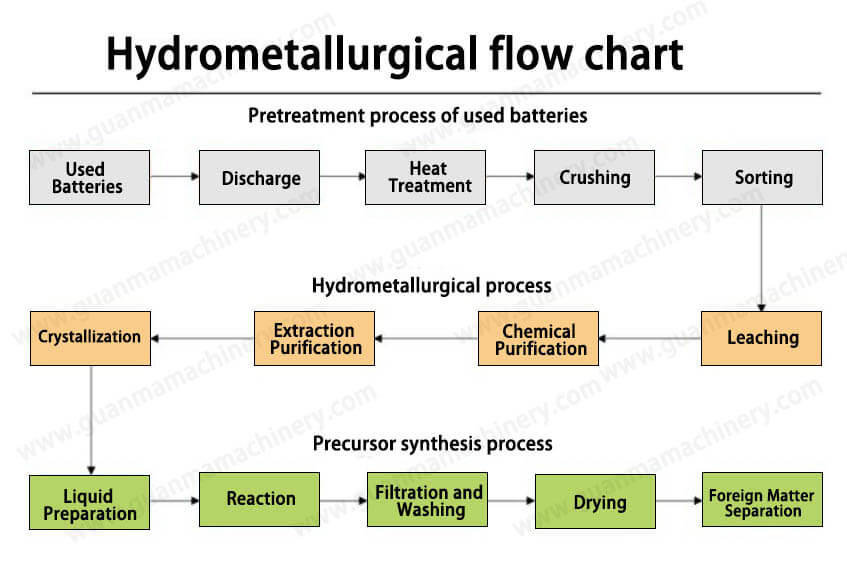
The ideal hydrometallurgical recycling approach involves converting spent lithium iron phosphate cathode material into lithium salts and ferric phosphate, achieving full elemental recovery of Li, Fe, and P. To transform lithium iron phosphate into lithium salts and ferric phosphate, ferrous must be oxidized to ferric iron, using acid leaching or alkali leaching to extract lithium.
Guanma Machinery Waste Lithium Battery Hydrometallurgical Recycling Process
1. Pre-treatment
Firstly, pre-treat the waste lithium batteries, including discharging, dismantling, crushing, and sorting;
2. Dismantling and Recycling
Recycle the plastic and iron casings after dismantling;
3. Acid Leaching
The sorted electrode materials undergo alkali leaching, acid leaching, impurity removal, followed by extraction;
4. Extraction
Extraction is a crucial step, separating copper from cobalt and nickel;
5. Electro-winning Reaction
Copper is sent to the electro-winning tank to produce electroplated copper products; the cobalt and nickel solutions post-extraction then undergo further separation through extraction. At this stage, through crystallization and concentration, cobalt salts and nickel salts are directly obtained; alternatively, the separated cobalt and nickel enter electro-winning tanks individually to obtain electroplated cobalt and electroplated nickel products. The recovery rates of cobalt, copper, and nickel in the electro-winning process reach 99%, with purities reaching 99.98%, 99.95%, and between 99.2% to 99.9% respectively. Products such as lithium sulfate and nickel sulfate all meet relevant standards.