Charcoal making machines have revolutionized the way charcoal is produced, offering an efficient, eco-friendly solution to meet the growing demand for high-quality charcoal. Whether you’re new to the concept or looking to optimize your existing setup, understanding how these machines work is essential.
What Is a Charcoal Making Machine?
Definition and Purpose
A charcoal making machine is a specialized device that converts biomass materials into charcoal through a process called carbonization. This machine provides a sustainable alternative to traditional methods, ensuring minimal environmental impact.
Types of Charcoal Making Machines
Charcoal making machines come in various types, including batch-type and continuous-type models. Each is designed to meet specific production capacities and operational needs.
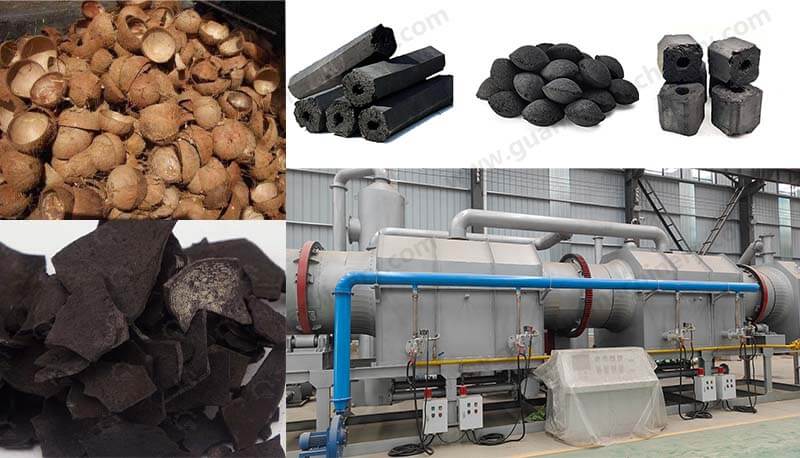
Key Components of a Charcoal Making Machine
Feedstock Feeder: Ensures a steady and safe supply of raw materials into the machine.
Carbonization Chamber: The core where biomass is converted into charcoal under controlled conditions.
Heat Source and Control System: Provides the necessary temperature for pyrolysis, often using biomass or gas as fuel.
Condenser System: Captures by-products like tar and wood vinegar for additional uses.
How Charcoal Making Machines Work
Step 1: Preparing the Raw Materials
Not all biomass is suitable for carbonization. Materials like wood chips, coconut shells, and sawdust are ideal. Pre-treatment involves drying the feedstock to reduce moisture content.
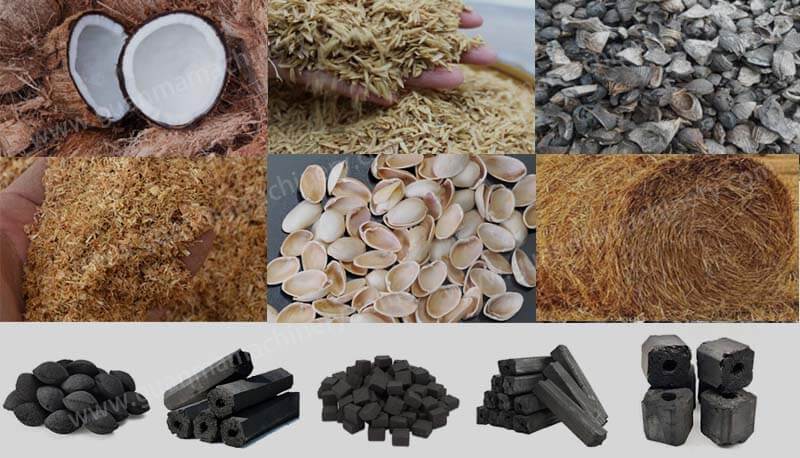
Step 2: Feeding the Machine
The prepared biomass is loaded into the feeder. Operators must follow safety protocols during this process to avoid accidents.
Step 3: Carbonization Process
This is the heart of charcoal production. The machine heats the biomass in an oxygen-free environment, causing pyrolysis. During this process, volatile gases are released, leaving behind carbon-rich charcoal.
Step 4: Collecting By-products
Apart from charcoal, the machine produces gas and tar. Advanced systems separate these by-products for additional applications, such as energy generation or industrial use.
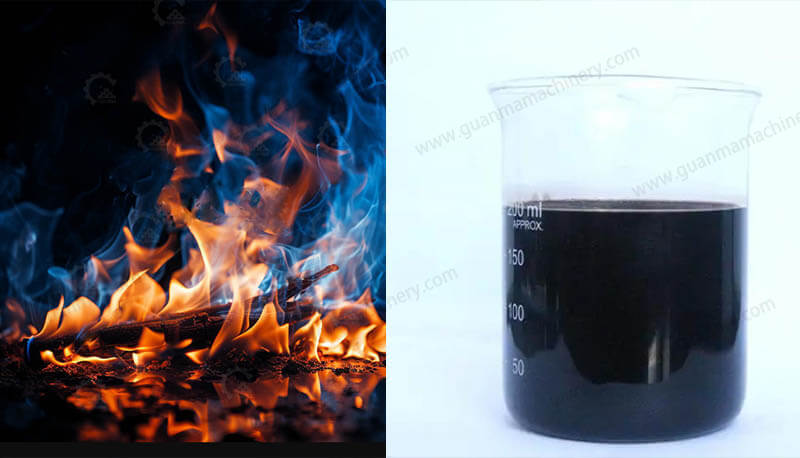
Step 5: Cooling and Packaging
The freshly produced charcoal is extremely hot and requires cooling before packaging. Proper storage ensures longevity and maintains quality.
Benefits of Using a Charcoal Making Machine
Charcoal making machines are a game-changer in many industries. They offer eco-friendly solutions, high energy efficiency, and the production of premium-quality charcoal, which is ideal for cooking, heating, and industrial purposes.
Applications of Charcoal Making Machines
From large-scale industrial applications to household uses, these machines cater to various needs. Industries use them for metallurgical processes, while households benefit from their efficiency in producing cooking fuel.
Maintenance Tips for Charcoal Making Machines
To keep your machine running smoothly, regular cleaning, lubrication, and inspection are essential. Replace worn-out components promptly to avoid operational hiccups.
Common Issues and Troubleshooting
Problems like uneven carbonization or heat distribution can arise. Addressing these issues promptly by checking settings and components ensures consistent output quality.
Cost and Investment Factors
While the initial cost may seem high, the ROI is significant due to reduced operating expenses and high-quality output.
Environmental Impact of Charcoal Making Machines
By utilizing biomass waste and minimizing emissions, these machines contribute to a greener planet. They reduce dependency on deforestation-driven charcoal production.
How to Choose the Right Charcoal Making Machine
Consider factors like production capacity, energy source availability, and certifications to ensure you choose a reliable and efficient machine.
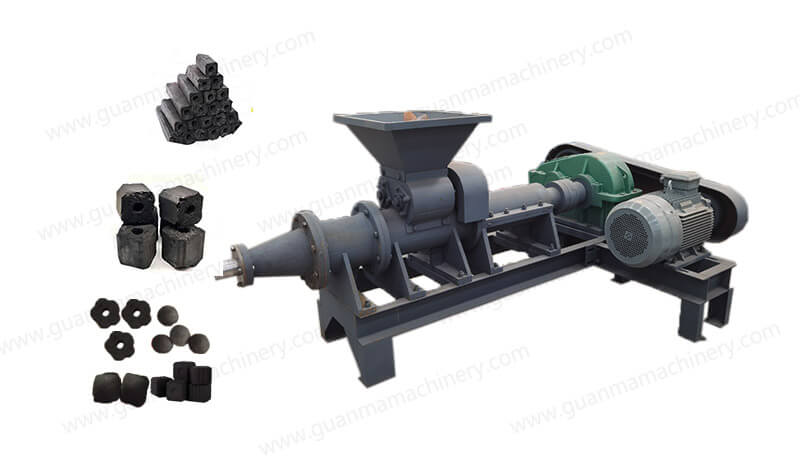
Future Trends in Charcoal Making Machines
Technological advancements are paving the way for smarter, more sustainable designs, making charcoal production even more eco-friendly and cost-effective.
Charcoal making machines are a vital innovation for sustainable energy production. Understanding their working mechanism not only helps in efficient usage but also contributes to a greener future.