Hydrometallurgy involves the chemical processing of cathode materials after mechanical disassembly of batteries. This method converts the cathode materials into ions through leaching, followed by separation, concentration, precipitation, and purification to generate metal salts or oxides. Hydrometallurgical processes operate at low temperatures, yielding products of high purity and efficiency, making it the predominant recycling method in China currently.
Hydrometallurgical process
The separation of valuable metals in this process primarily relies on dissolution and leaching. The effectiveness of leaching significantly impacts the overall recovery rate of metallic elements. Factors influencing leaching efficiency include the composition and concentration of the leaching solution, as well as the temperature, duration, and ratio of materials during the leaching process. Commonly employed leaching methods in hydrometallurgical recovery include acid leaching, combined acid and oxidant leaching, and bioleaching.
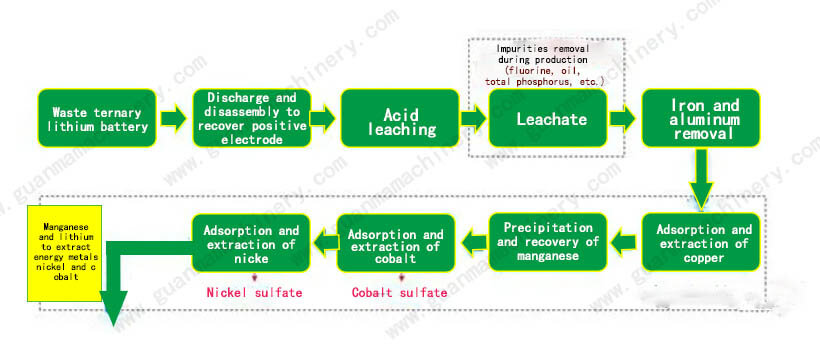
Hydrometallurgical process leaching
In a detailed hydrometallurgical process, after the batteries have been mechanically shredded and the cathode materials separated, they undergo leaching where the metals are dissolved into a liquid medium. This is often achieved using acids, such as sulfuric acid, nitric acid, or hydrochloric acid, sometimes in combination with oxidizing agents like hydrogen peroxide or chlorine dioxide to enhance the solubility of certain metals. Bioleaching utilizes microorganisms to catalyze the leaching process, particularly useful for metals that are difficult to dissolve under conventional conditions.
Following leaching, the solution is treated to precipitate the desired metals, often through pH adjustment or the addition of reagents that cause the metals to precipitate out of the solution as solids. These precipitates can then be filtered, washed, and dried before undergoing further processing to refine them into usable forms, such as metal salts or oxides suitable for reuse in battery manufacturing or other applications. This multi-step process allows for the selective recovery of specific metals from the complex mixture found in battery cathodes, maximizing resource utilization and reducing waste.