Hydrometallurgy is a process used to extract many metals and compounds from their ores. It plays a significant role in industries dealing with zinc, aluminum, copper, uranium, and others. Currently, the entire global production of alumina and uranium oxide, about 74% of zinc, and nearly 12% of copper are produced through hydrometallurgical processes.
Hydrometallurgy consists of the following steps:
1. Leaching: The valuable components of the ore are dissolved into a solution.
2. Solid-Liquid Separation: The leached solution is separated from the residue, and any entrained metallurgical solvent and metal ions carried over with the residue are recovered through washing.
3. Solution Purification and Concentration: Often utilizing ion exchange and solvent extraction techniques, or other chemical precipitation methods, the leached solution is purified and enriched.
4. Metal or Compound Recovery: The metal or compound is extracted from the purified solution.
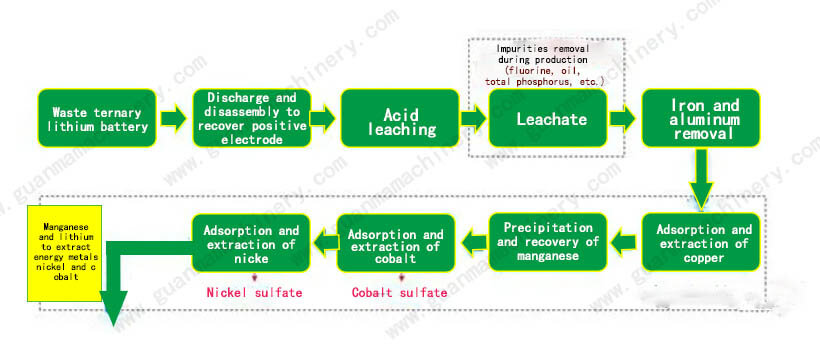
In industrial practice, electrolysis is commonly employed to extract pure metals such as gold, silver, copper, zinc, nickel, and cobalt from the purified solutions. Metals like aluminum, tungsten, molybdenum, and vanadium, which exist primarily as oxo-acids in aqueous solutions, are usually precipitated as oxides first, then reduced to obtain the metals.
Hydrometallurgical Process
High-pressure hydrometallurgical techniques, developed in the 1950s, allow for the direct reduction of metals like copper, nickel, and cobalt from ammoniacal solutions using hydrogen (for example, at 180°C and 25 atmospheres). This process yields metal powders of copper, nickel, and cobalt, as well as a variety of superior composite metal powders, such as nickel-coated graphite and nickel-coated diatomaceous earth. These are excellent materials for applications requiring grindable seals and thermal spray coatings.