The rapid growth of electric vehicles (EVs) and renewable energy storage systems has led to an unprecedented surge in lithium-ion battery production. However, this boom also raises critical challenges: how to recycle end-of-life batteries efficiently while recovering valuable metals sustainably? Hydrometallurgy battery recycling emerges as a groundbreaking answer, offering a cleaner, more efficient alternative to traditional pyrometallurgical methods.
1. What Is Hydrometallurgy Battery Recycling?
Hydrometallurgy is a specialized process that uses aqueous chemistry to extract and purify metals from spent lithium-ion batteries. Unlike energy-intensive pyrometallurgy, which relies on high-temperature smelting, hydrometallurgical methods dissolve battery components in targeted chemical solutions. This enables precise recovery of high-purity metals like lithium, cobalt, nickel, and manganese—critical for producing new batteries.
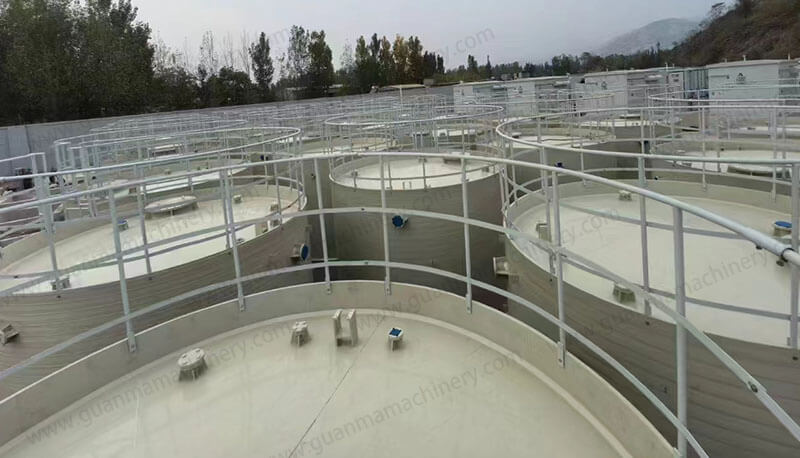
2. Advantages of Hydrometallurgical Recycling Over Traditional Methods
A. Higher Metal Recovery Rates
Hydrometallurgy achieves recovery rates exceeding 95% for cobalt, nickel, and lithium, compared to pyrometallurgy’s 50–70%. This efficiency reduces reliance on mining virgin materials, aligning with circular economy principles.
B. Lower Environmental Impac
By avoiding high-temperature operations, hydrometallurgy slashes greenhouse gas emissions by up to 40% and minimizes toxic fumes. Water-based processes also allow closed-loop systems, reducing wastewater pollution.
C. Cost-Effectiveness for Rare Metals
With cobalt prices fluctuating and lithium demand soaring, hydrometallurgy’s ability to recover high-purity metals cost-effectively makes it ideal for EV and electronics manufacturers seeking supply chain stability.
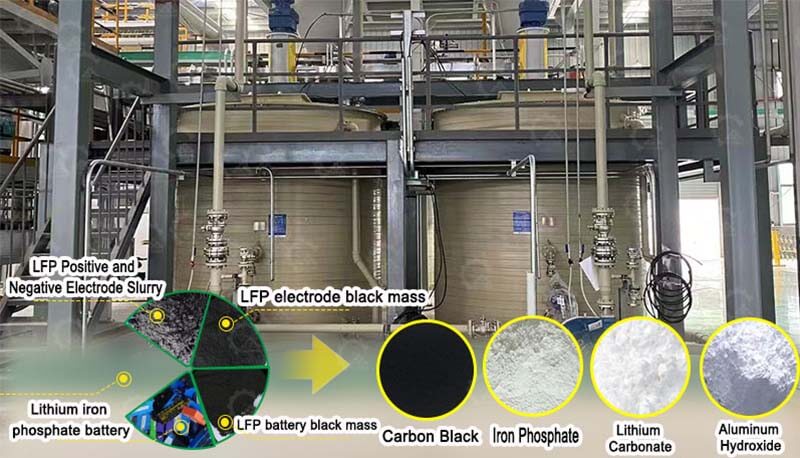
3. The Hydrometallurgical Process: Step-by-Step
1. Battery Pre-Treatment: Safe discharging, dismantling, and mechanical crushing to separate black mass (metal-rich material).
2. Leaching: Black mass is dissolved in acidic or alkaline solutions (e.g., sulfuric acid) to extract metals into a liquid phase.
3. Purification: Impurities like aluminum or copper are removed via precipitation, solvent extraction, or ion exchange.
4. Metal Recovery: Target metals are electrochemically or chemically precipitated as salts or oxides, ready for reuse.
Innovative applications:
Selective leaching for mixed battery chemistries (NMC, LFP)
Integration with AI for real-time process optimization
4. Why Hydrometallurgy Supports Global Sustainability Goals
The International Energy Agency (IEA) estimates that recycling could supply 10–30% of lithium, cobalt, and nickel needs by 2040. Hydrometallurgy directly contributes to:
Reduced mining pressure: Recycling 1 ton of lithium batteries saves 5 tons of mined ore.
Lower carbon footprint: Recovered metals generate 70% fewer emissions than virgin materials.
Regulatory compliance: Meets EU Battery Regulation and U.S. Inflation Reduction Act standards for recycled content.
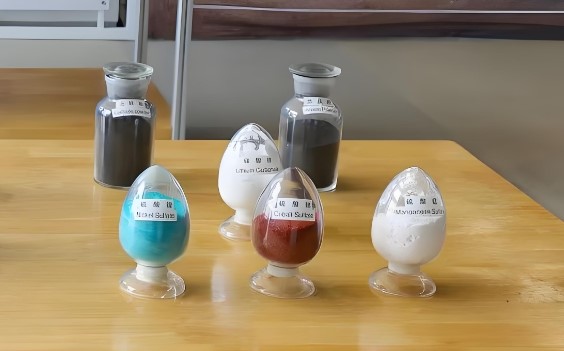
5. Partnering with a Hydrometallurgy Recycling Expert
To maximize ROI from battery recycling, collaborate with providers offering:
Customized chemical formulations for diverse battery types.
Scalable modular systems adaptable to regional demands.
Case study: A European recycler reduced processing costs by 25% using AI-driven hydrometallurgical systems, achieving 98% cobalt purity.
Embrace Hydrometallurgy for a Greener Battery Economy
Hydrometallurgy battery recycling isn’t just a technology—it’s a necessity for sustainable energy transitions. By recovering critical metals efficiently and eco-consciously, businesses can future-proof their operations while meeting ESG targets.