In an era defined by rapid technological advancement and increasing environmental consciousness, the recycling of lithium-ion batteries (LIBs) has become a critical component of sustainable manufacturing. Among various methods for recycling these batteries, hydrometallurgical processes stand out due to their efficiency and eco-friendliness. This article delves into the specifics of hydrometallurgical battery recycling, focusing on the key steps involved in this innovative technique.
Understanding Hydrometallurgical Processes
Hydrometallurgy is a branch of extractive metallurgy that uses aqueous solutions to separate and recover metals from ores or waste materials. In the context of lithium battery recycling, hydrometallurgical processes involve several stages designed to extract valuable metals such as lithium, cobalt, nickel, and manganese from spent LIBs. These processes not only reduce waste but also contribute significantly to the circular economy by recovering and reusing these precious resources.
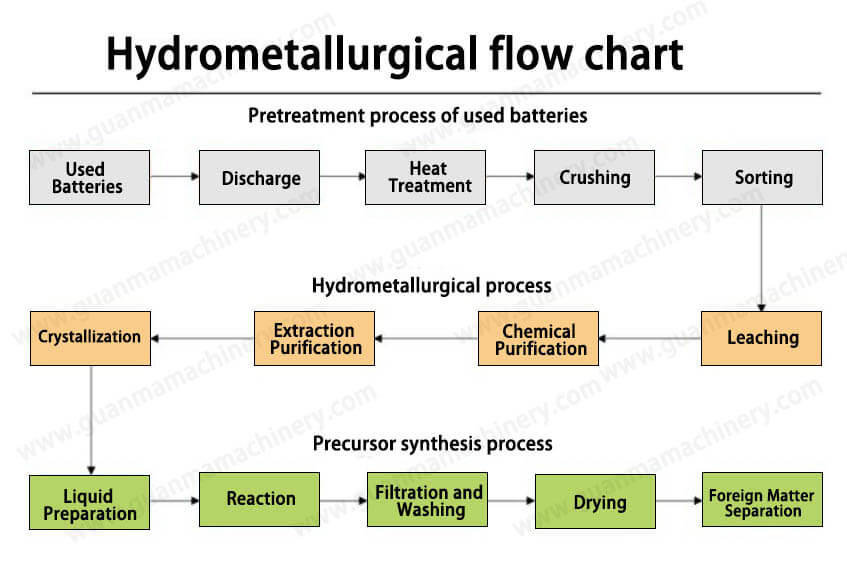
The Hydrometallurgical Battery Recycling Process
1. Pre-treatment
Before the actual hydrometallurgical extraction begins, spent batteries undergo pre-treatment to ensure they are safe and ready for processing. This stage includes:
Discharging: Ensuring all electrical energy is discharged.
Shredding: Breaking down the batteries into smaller pieces to increase surface area and facilitate extraction.
Separation: Separating plastics, steel casings, and other non-metallic components from the metallic fraction.
2. Leaching
Leaching is a critical step where the metallic components are dissolved using a suitable leaching agent. Common leaching agents include sulfuric acid, hydrochloric acid, and sodium carbonate, depending on the specific metals being targeted. The leaching process dissolves valuable metals while leaving behind insoluble materials like aluminum and copper foils.
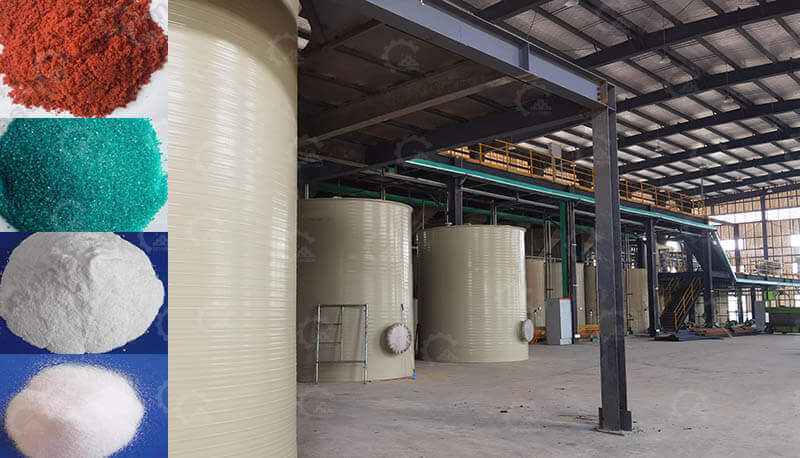
3. Metal Recovery
After leaching, the solution contains dissolved metals, which need to be recovered through precipitation, solvent extraction, or ion exchange techniques. For example:
Precipitation: Adding chemicals to the solution to form solid compounds that can be filtered out.
Solvent Extraction: Using organic solvents to selectively extract certain metals based on their solubility characteristics.
Ion Exchange: Utilizing resins that selectively bind to specific ions, allowing them to be separated from the solution.
4. Refining and Purification
The recovered metals are further refined and purified to meet industry standards. This may involve additional chemical treatments or electrolysis to produce high-purity metals suitable for reuse in new batteries or other applications.
Advantages of Hydrometallurgical Processe
Environmental Impact: Hydrometallurgical processes generally require less energy compared to pyrometallurgical methods and produce fewer emissions.
Economic Viability: By recovering valuable metals, these processes offer a cost-effective alternative to mining new raw materials.
Flexibility: The process can be adapted to recover multiple metals simultaneously, making it versatile for different types of lithium batteries.
As demand for lithium-ion batteries continues to soar, the importance of sustainable recycling practices cannot be overstated. Hydrometallurgical processes provide a viable solution for extracting and recovering valuable metals from spent batteries, contributing to both economic and environmental sustainability. By embracing these advanced recycling technologies, we can pave the way for a more responsible and efficient use of resources in the global battery industry.