Delve into the key differences between pyrometallurgical vs hydrometallurgical treatments for ternary lithium batteries. Learn which process best suits your recycling needs.
Pyrometallurgy vs Hydrometallurgy
In the rapidly evolving landscape of battery technology, the recycling of spent ternary lithium-ion batteries has become a critical concern. These batteries, characterized by their use of a combination of nickel, cobalt, and manganese in their cathodes, offer significant advantages in terms of energy density and performance. However, their disposal and recycling require careful consideration to ensure the recovery of valuable metals and to mitigate environmental impacts. This article explores the fundamental differences between two primary recycling methods: pyrometallurgy and hydrometallurgy.
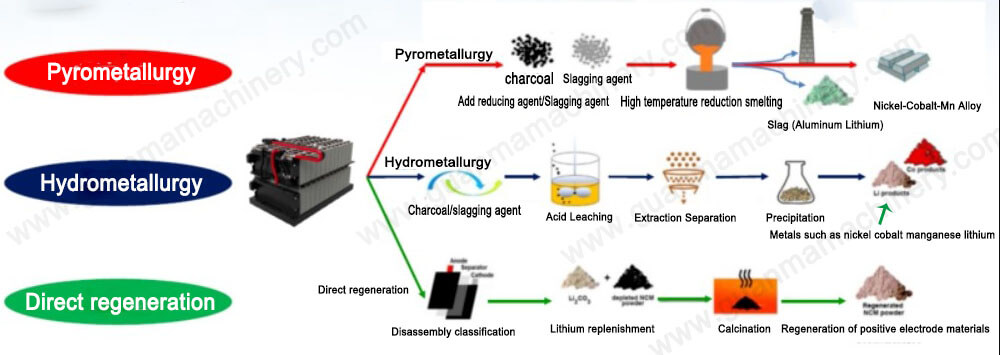
Pyrometallurgy: The Heat of Transformation
Pyrometallurgy, often referred to as ‘fire refining’, is a high-temperature process that involves the incineration of spent batteries to melt and separate the constituent metals. This method is particularly effective in removing organic materials and impurities through combustion.
The process typically involves several stages:
Shredding and Drying: Batteries are first shredded and dried to remove moisture and reduce the risk of fires during the high-temperature treatment.
Smelting: The dried material is then heated in a furnace, causing the metals to melt and separate from the non-metallic components.
Slagging and Metal Pouring: Non-metallic residues form slag, which is skimmed off, leaving behind molten metals that can be poured and cooled to form ingots.
Advantages of Pyrometallurgy
High-Temperature Purification: Pyrometallurgy effectively purifies metals by removing organic compounds and other contaminants.
Energy Intensive but Efficient: While requiring significant amounts of energy, the process yields high-purity metals.
Hydrometallurgy: The Liquid Pathway to Recovery
Hydrometallurgy, on the other hand, employs aqueous solutions to leach metals from the battery waste. This process is more nuanced and can be tailored to target specific metals with greater selectivity. Key steps in hydrometallurgical treatment include:
Crushing and Leaching: Spent batteries are crushed and mixed with a leaching agent, typically an acid or a base, to dissolve the metals.
Solid-Liquid Separation: The leached solution is separated from the insoluble materials through filtration or centrifugation.
Metal Recovery: The dissolved metals are recovered through precipitation, solvent extraction, or electrowinning.
Advantages of Hydrometallurgy
Selective Metal Recovery: Hydrometallurgy allows for the selective recovery of individual metals, making it ideal for the recovery of lithium, nickel, cobalt, and manganese.
Lower Energy Consumption: Compared to pyrometallurgy, hydrometallurgy consumes less energy and produces fewer greenhouse gas emissions.
Choosing the Right Process for You
Deciding between pyrometallurgy and hydrometallurgy for recycling ternary lithium batteries depends on several factors, including the desired purity of the recovered metals, the scale of operations, and environmental considerations. For recyclers aiming for high-purity metals with less concern for energy efficiency, pyrometallurgy might be the preferred choice. Conversely, those prioritizing lower energy consumption and selective metal recovery might lean towards hydrometallurgy.
Whether you opt for the fiery transformation of pyrometallurgy or the aqueous precision of hydrometallurgy, understanding the nuances of each process is crucial to optimizing your ternary lithium battery recycling efforts. Both methods have their merits and drawbacks, and the right choice will depend on your specific goals and constraints. By staying informed about these processes, you can make an educated decision that aligns with your recycling objectives and contributes to a more sustainable future.