In the fast-paced world of precious metal recovery, efficiency and precision are non-negotiable. Whether you’re a jeweler, electronics recycler, or mining company, silver refining equipment is the backbone of transforming raw materials into high-purity silver. But with varying technologies, costs, and suppliers, how do you choose the right solution?
Why Invest in Modern Silver Refining Equipment?
Silver refining is a complex process that demands accuracy to recover maximum metal value while minimizing waste. Traditional methods, like cupellation or nitric acid dissolution, are labor-intensive and pose environmental risks. Modern silver refining systems, however, offer:
Higher Purity Output: Achieve 99.99% pure silver with electrolytic or chemical refining.
Reduced Chemical Consumption: Closed-loop systems recycle acids and solvents, cutting costs by up to 40%.
Faster Processing: Automate tasks like filtration and drying to refine 50–100 kg of silver daily.
For businesses scaling operations, upgrading to silver electrolytic refining equipment is a strategic move to stay competitive.
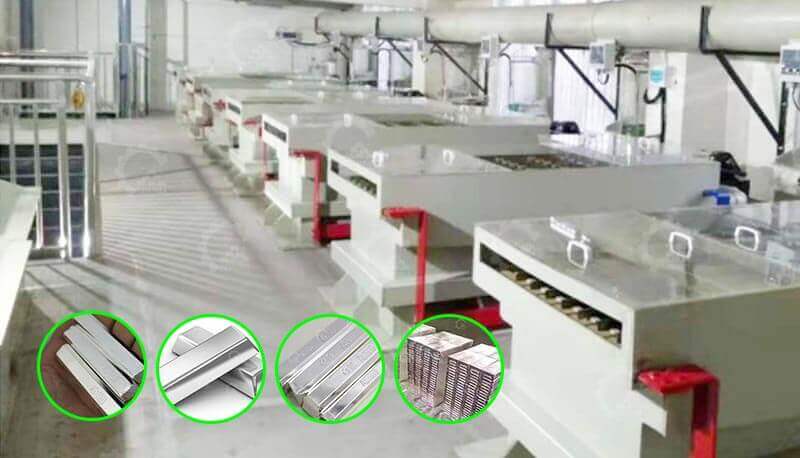
Key Steps in the Silver Refinery Process
Understanding the workflow helps identify the right machinery. Here’s a simplified breakdown:
1. Dissolution: Raw silver (e.g., scrap, ore) is dissolved in nitric acid or a cyanide solution.
2. Filtration: Impurities like gold or platinum are removed using filter presses or centrifuges.
3. Precipitation: Silver is precipitated as silver chloride or through electrolysis.
4. Melting & Casting: Pure silver is melted in induction furnaces and cast into bars or granules.
Each stage requires specialized equipment. For example, a silver electrolytic refining machine uses anodes and cathodes to separate silver from other metals, ideal for high-volume operations.
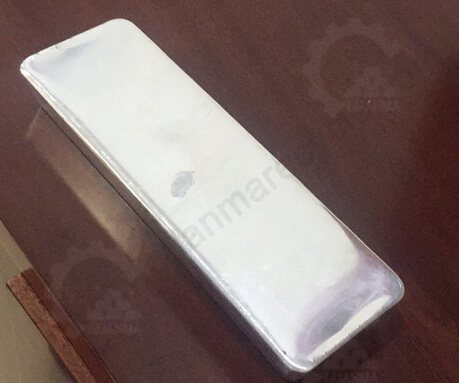
How to Choose the Silver Refining Equipment: 5 Factors
When comparing silver refinery machine prices, prioritize these features to avoid costly mistakes:
1. Capacity & Scalability
Match equipment to your daily throughput. Small-scale units (1–10 kg/day) suit jewelers, while industrial systems (100+ kg/day) fit recyclers.
2. Automation Level
Semi-automatic systems reduce labor costs, while fully automated PLC-controlled machines ensure consistency for ISO-certified refineries.
3. Material Compatibility
Ensure the equipment handles your input materials (e.g., silver nitrate solutions, jewelry scraps, or PCB boards).
4. Energy Efficiency
Look for induction melters with 90%+ thermal efficiency or electrolytic cells with low power consumption.
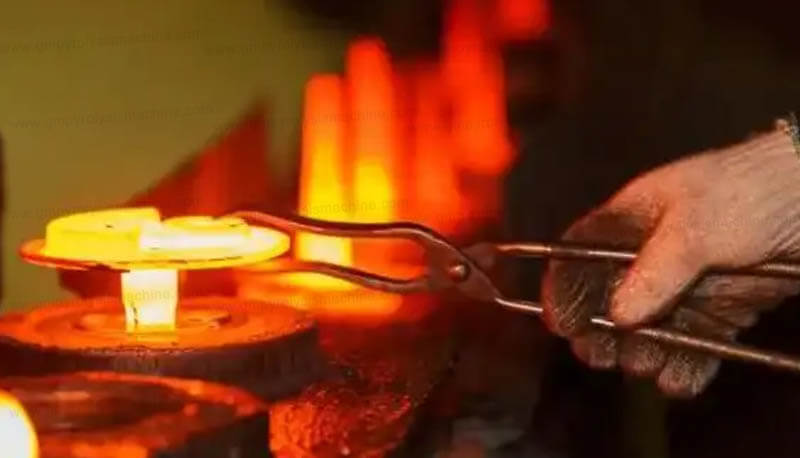
5. After-Sales Support
Reputable silver refinery machine manufacturer provide installation, operator training, and spare parts access.
Lower Operational Costs: Energy-efficient machines reduce power bills by 20–30%.
Higher Recovery Rates: Filtration can reclaim 98% of silver vs. 85% in manual setups.
Durability: Stainless steel or titanium-coated components last 5–10 years, minimizing replacements.
Always request a ROI analysis from suppliers to justify upfront investments.
Top Applications of Silver Refining Equipment
Jewelry Recycling: Convert broken or outdated pieces into pure silver for new designs.
Electronics Waste: Extract silver from connectors, switches, and solders in e-waste.
Mining: Refine silver concentrates from ore to meet LBMA standards.
Photography: Recycle silver from X-ray films or photographic chemicals.
Investing in the right silver refining equipment is pivotal to unlocking profitability in the precious metals industry. By prioritizing advanced technology, supplier reliability, and eco-friendly practices, you can streamline the silver refinery process while future-proofing your operations.