If you’re in the precious metals industry, understanding silver refining machine cost is critical to maximizing profits and ensuring efficient operations. Whether you’re a jewelry manufacturer, e-waste recycler, or mining company, the right silver refining equipment can transform raw materials into 99.99% pure silver—but upfront investments and hidden expenses often raise questions.
Why Invest in a Silver Refining Machine?
Silver refining is essential for:
Recovering high-purity silver from scrap, jewelry, electronics, or mining byproducts.
Reducing reliance on third-party refiners, saving 20–40% in processing fees.
Meeting industrial standards for applications like solar panels, medical devices, and bullion production.
However, the cost of refining silver depends heavily on your chosen technology, capacity, and supplier. Let’s explore the options.
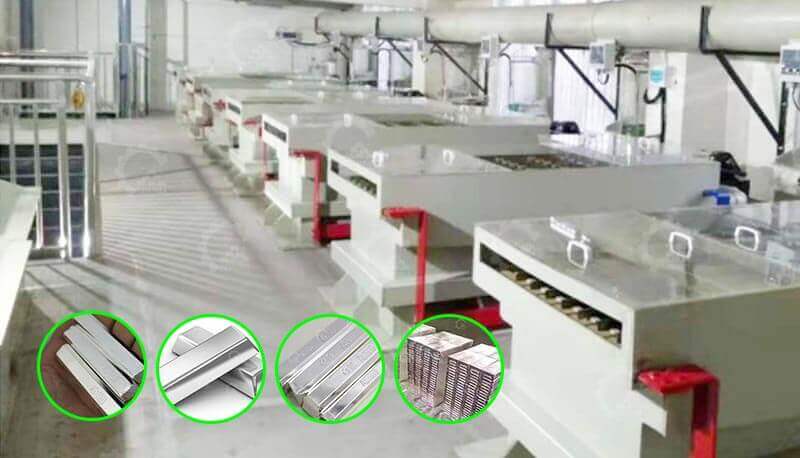
Types of Silver Refining Equipment & Their Costs
1. Electrolytic Refining Systems
Process: Uses electrolysis to separate silver from impurities.
Best for: High-volume operations (100+ kg/day).
Silver refining machine cost: $50,000–$250,000+
Budget Tip: Opt for modular systems to scale capacity as demand grows.
2. Chemical Leaching Plants
Process: Dissolves silver with nitric acid or cyanide, then precipitates pure metal.
Best for: Small to medium-scale refiners (10–50 kg/day).
Equipment cost: $20,000–$80,000
Caution: Factor in waste treatment systems ($10,000–$30,000) to comply with environmental laws.
3. Induction Melting Furnaces
Process: Melts and purifies silver alloys using high-frequency induction.
Best for: Jewelers and artisans refining silver onsite.
Cost: $5,000–$15,000
Limitation: Purity typically caps at 99.5%, requiring secondary refining for higher grades.
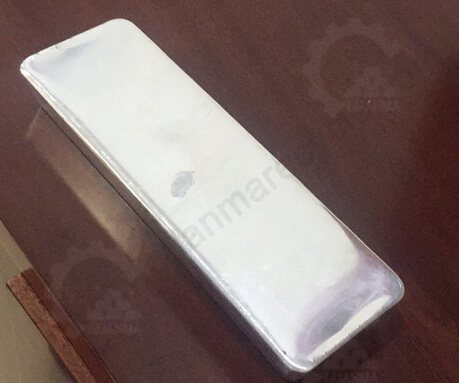
Key Factors Affecting Silver Refinery Machine Prices
1. Capacity
Small-scale machines (1–10 kg/day): $5,000–$30,000
Industrial systems (100–1,000 kg/day): $80,000–$500,000
2. Automation Level
Manual systems: Affordable ($5k–$20k) but labor-intensive.
Fully automated silver refining systems: Higher upfront cost ($50k–$300k) but reduce labor by 70%.
3. Material Compatibility
Machines handling e-waste (PCBs, connectors) cost 20–30% more due to added shredding and sorting modules.
4. Energy Efficiency
Energy-saving models cut power costs by 40% but add $15k–$50k to the price.
Hidden Costs to Consider
Installation & Training: $3,000–$20,000, depending on complexity.
Consumables: Acids, filters, and electrodes cost $1,000–$5,000 annually.
Maintenance: Budget 5–10% of the machine’s price yearly for parts and servicing.
How to Reduce Silver Refining Machine Costs
1. Buy Refurbished Equipment
Save 30–50% by purchasing certified systems from reputable suppliers.
2. Choose All-in-One Systems
Integrated silver refining machines with built-in pollution controls minimize auxiliary costs.
3. Negotiate Supplier Packages
Many manufacturers offer discounts on bulk orders or multi-year service contracts.
Choosing a Reliable Silver Refining Equipment Supplier
1.Certifications
Ensure ISO 9001, CE, or EPA compliance for quality and safety.
2. After-Sales Support
Prioritize suppliers offering 24/7 technical assistance and spare parts.
3. Customization
Look for manufacturers who tailor systems to your feedstock.