The hydrometallurgical process of leaching is a widely used technique in the field of metallurgy and material extraction. It involves the use of chemical solutions to dissolve valuable metals from ores, concentrates, or secondary sources like recycled materials. This method is favored for its ability to extract metals in an environmentally friendly and cost-effective manner compared to traditional smelting techniques.
Understanding the Leaching Process
Leaching is a key step in hydrometallurgy, where a specific solvent is introduced to separate metals from their surrounding materials. The process typically includes the following stages:
Preparation of the Material
The ore or raw material is crushed and ground into fine particles to increase the surface area for better interaction with the leaching solution.
Leaching
The prepared material is exposed to a leaching agent, such as acids (sulfuric acid, hydrochloric acid) or bases (ammonia), depending on the type of metal being extracted. For example:
Acid leaching is commonly used for copper and zinc extraction.
Cyanide leaching is used for precious metals like gold and silver.
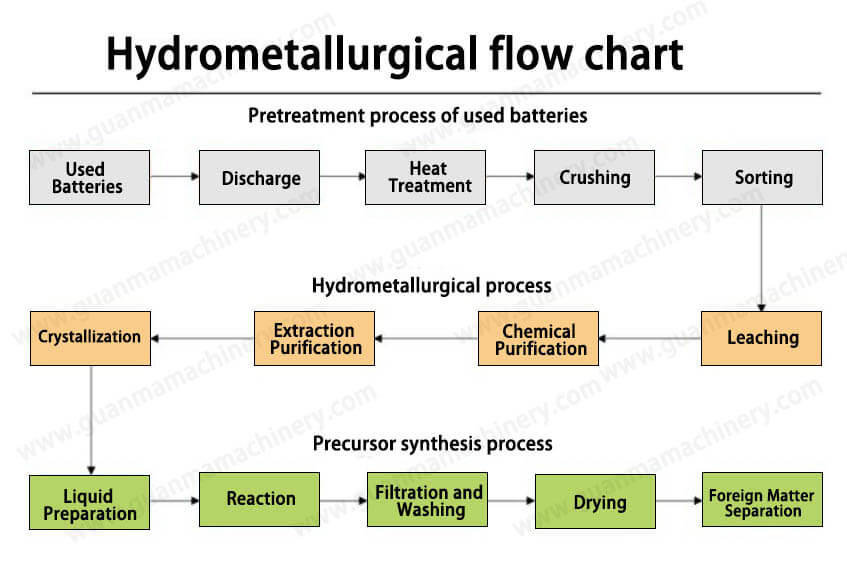
Separation and Recovery
The solution containing the dissolved metals, known as the leachate, is separated from the solid residues. Further chemical or physical processes, such as precipitation, solvent extraction, or electrolysis, are employed to recover the metal in pure form.
Waste Management
The leftover materials, or tailings, are managed to minimize environmental impact.
Types of Leaching Processes
Heap Leaching
This method involves stacking crushed ore into heaps and applying the leaching solution from the top. The solution trickles through the heap, dissolving the metals as it moves downward. This technique is commonly used for low-grade ores.
Tank Leaching
In this controlled method, ore is placed in tanks and agitated with the leaching solution, providing higher efficiency and faster recovery compared to heap leaching.
In-Situ Leaching
This innovative method involves injecting the leaching solution directly into the ore deposit underground, extracting metals without the need for mining.
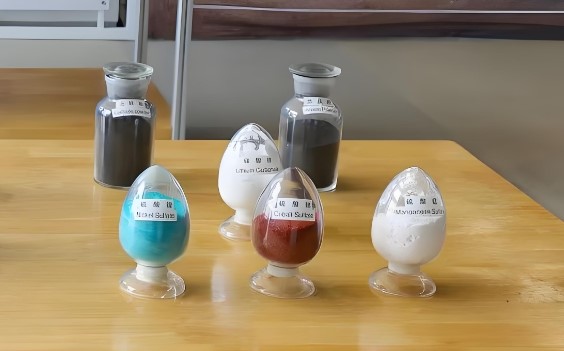
Advantages of the Leaching Process
Eco-Friendly: Unlike traditional methods that emit harmful gases, leaching has a lower environmental footprint.
Efficient for Low-Grade Ores: It allows for the economic extraction of metals from ores with low concentrations of valuable minerals.
Flexibility: The process can be tailored to extract a wide variety of metals, including copper, gold, silver, nickel, and uranium.
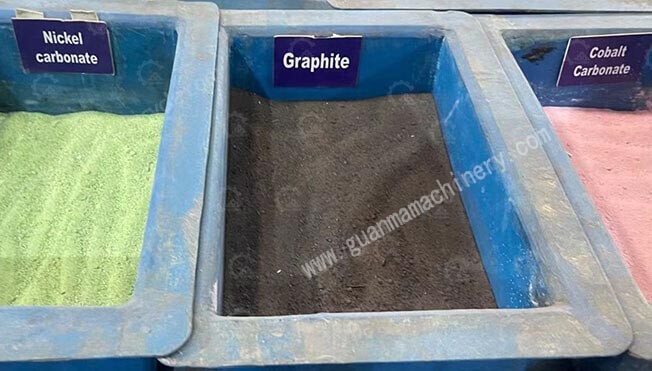
Challenges and Limitations
Despite its benefits, the hydrometallurgical process has some challenges:
Chemical Usage: Large quantities of chemicals may pose handling and disposal challenges.
Time-Consuming: Certain types of ores may require prolonged leaching durations.
Environmental Concerns: Improper waste management can lead to contamination of soil and water.
Conclusion
The hydrometallurgical process of leaching is a vital technique in modern metallurgy, providing an effective way to extract metals from various materials. By continuing to refine and develop this technology, industries can benefit from its economic and environmental advantages while addressing its challenges.